Special ground engineering work for a multibillion-euro high-speed train line is Keller Grundbau’s largest ever contract win in Austria. With the €32 million project well underway, we talk to Christoph Deporta about how newly developed technology is dramatically increasing production on a complex site.
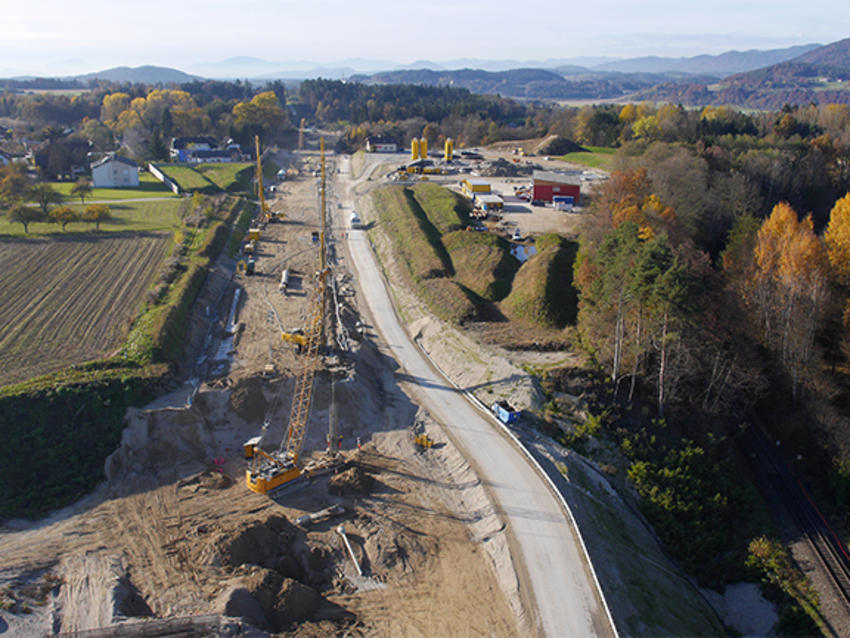
Once completed in 2023, the Koralm rail line will reduce travel time between the cities of Graz and Klagenfurt from three hours to less than one. It'll also form part of a 2,400km trans-European line stretching from the northern coast of Poland to northern Italy, linking the Baltic and Adriatic seas.
Keller Grundbau is playing an important role in the project, carrying out ground engineering works on two tunnels in the St Kanzian area – believed to be one of the biggest construction challenges on the Koralm railway line.
Keller was chosen by the project’s main construction teams, Kostmann and German tunnelling specialists Baresel. The contract is our largest ever in Austria and began with trials in March 2015.
So far, so good
Work on the first tunnel – being built using a cut-and-cover method – is now complete. It involved constructing bored piles as a retaining wall on either side of the tunnel to a depth of 22m. Soilcrete columns were then added to reinforce the bottom of the excavation and ceiling columns added between the bored piles.
Piling has also started on the second tunnel, Untersammelsdorf. This will also include Soilcrete columns and is scheduled to be finished in February 2018. When the entire project is complete, we’ll have constructed around 2,000 1.2m diameter bored piles totalling 58,000m, and 75,000m of Soilcrete columns, 1.5m in diameter. Anchors, nails and shotcrete are also being used.
“Not only is this a very large project, but it’s also unique because of the difficult soil conditions,” explains Christoph Deporta, who until recently was the project manager. “In many areas there are silty still-water sediments – lacustrine clays – making the ground inconsistent, and ranging from soft to semi-solid. The conditions were not ideal so first we had to execute three trial fields in different areas of the site and soil conditions to show the client we could guarantee the diameter and strength of the Soilcrete columns.”
Super-efficient equipment
A key to success of this project was also the use of new-generation Keller rigs (KB6) , pumps (TW700), monitors and nozzles. Christoph says that the new equipment makes Soilcrete construction more efficient, allowing them to jet grout faster, with less cement and less disposal cost, without compromising strength.
All rigs on site are also using GPS technology to position the columns, which has doubled the speed of relocation and construction. The new equipment and a lot of other improvements allows the team to use just two rigs instead of four.
So far the client is incredibly happy with the progress Keller has made and the project is well on schedule. Once again, Keller is demonstrating how our people rise to the challenge, no matter how big or demanding a project.