What do you do when the ground you need to drill can't be reliably checked for unexploded ordnance? When Keller Grundbau faced this problem on one of Europe’s biggest projects, we came up with an unusual idea: freezing the ground with liquid nitrogen.
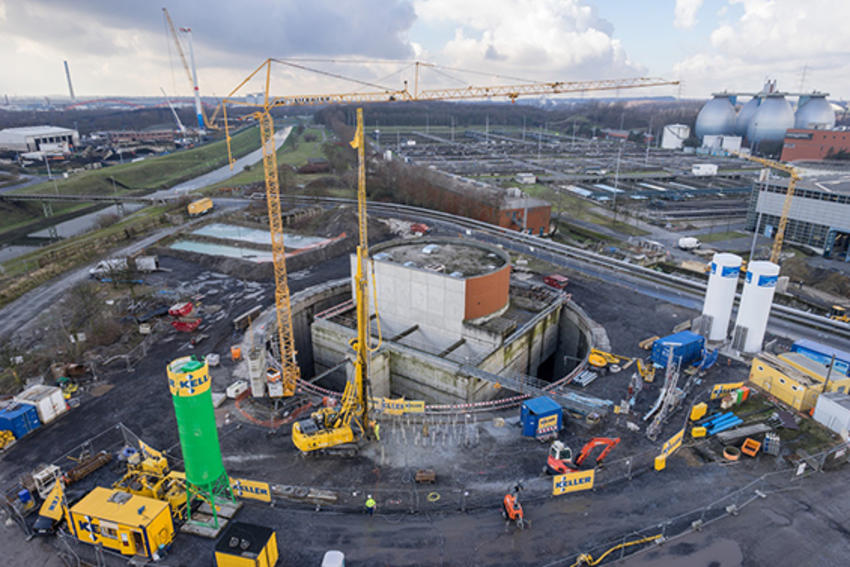
For more than a century, the River Emscher in western Germany has been called Europe’s foulest river; a dumping ground for industrial and municipal waste. But since the 1990s, the Emscher has been subject to a massive €4.5 billion renaturation project.
Sewage pumping stations have been built and a vast underground tunnelling system is under construction to divert waste water from the river. The tunnels run 73km from Dortmund to where the Emscher meets its famous big brother, the Rhine, and are scheduled for completion in 2020.
A tricky problem unearthed
One of the sewage stations is in the city of Bottrop and it was here in September 2015 that Keller Grundbau was brought in for a challenging design-and-build project. The client (waste water management company Emschergenossenschaft Essen) needed to connect the pumping station with the tunnel using microtunnelling (1,800mm in diameter at a depth of about 19m).
Our task was to create the initial 1.250m3 sealing block directly beneath the wall outside the shaft. This solid cube was needed so that the boring machine could begin drilling through without the tunnel collapsing due to earth and water pressure. But there was a problem, as Department Manager Frank Ludwig explains: “Originally the plan was to use traditional jet-grouting, but because the ground couldn’t reliably be checked for unexploded ordnance, we weren’t able to get official approval.”
Undeterred, the team had to find another way. Working with the client and technical consultants, they came up with the idea of using liquid nitrogen, carefully pumped in to freeze the ground and create the sealing block.
Precision engineering
“Although a similar technique had been used on a couple of projects in the past, as far as we’re aware nothing as complex as this had been tried before,” says Frank. “Working with suppliers Linde AG of Düsseldorf, we drilled more than 55 highly precise boreholes with a diameter of less than 120mm to a depth of nearly 30m – all the while guided by a bomb expert. The holes had to be very close together and incredibly straight, with less than one percent vertical deviation. We inserted the dense copper pipes into these to inject liquid nitrogen and freeze the soil and groundwater.”
Added to the challenge, the team had to consider the different ground layer conditions, which included soft, sludgy backfill, sand and clay. Furthermore, the soil was contaminated, requiring workers to wear special high-standard protective masks and clothing. Special thermic pipes with sensors were used to measure the temperatures needed for approving the size of the freezing block in the different soils.
Once frozen, the block was actually too cold for the drilling machine. Therefore, the temperature had to be raised slightly from between -195ºC and -140ºC to between -20ºC and -10ºC. In total, this meticulous operation took more than four months to freeze the soil and maintain it until the end of the tunnelling – but it worked.
“The project was a success and we had very good feedback from the client,” Frank says. “What’s more, the client can now use this technique in similar circumstances on future projects. We’ve shown how we can work with the client, contractor, suppliers and technical consultants to overcome an extremely challenging situation with an innovative solution on a very high-profile project. Our experience, special equipment, mechanical engineering expertise and ability to deliver such a complex project to satisfaction has really distinguished us from the competition.”