As increasing land shortages drive developers towards more brownfield and marginal sites, there's greater demand than ever for our business units to offer a wider range of innovative geological techniques. A great example is Keller company Franki Africa, which recently tapped into global expertise to offer Columns with Mixed Moduli (CMM®).
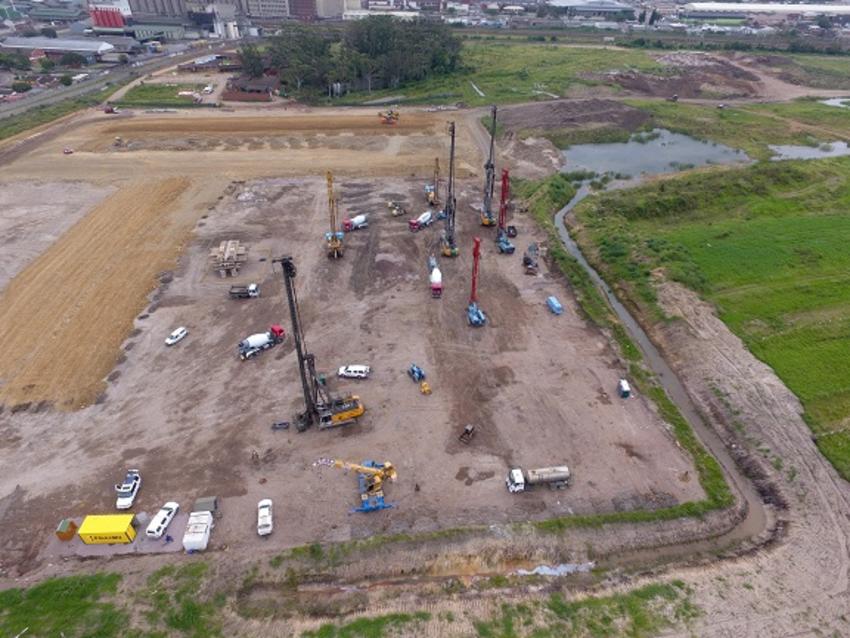
This ground-improvement technology developed by Keller combines rigid inclusions and a stone column head, carried out with a bottom-feed vibrator system.
Durban’s former racecourse is being transformed into a 368,000m2 logistics site to service the city’s bustling container port, one of the busiest in the world.
When it’s completed in 2019, the Clairwood Logistics Park will house seven platforms for warehousing, ranging from 25,000m2 to 130,000m2. However, with the site underlain by soft clays up to 38m deep, project consultants Bigen Africa required specialist help to stabilise the ground, so turned to Franki Africa.
Developing a solution
“Working closely with the client, we started our investigations. We initially looked at traditional piling, but this wasn’t financially feasible due to the depths required,” explains Victor Ferreira, Franki Business Development Manager. “You have to go quite deep to find a competent soil layer and under those soft, compressible clays we would have had to use casings, which would have made the production slow and expensive.
“We spoke to our Keller colleagues in Offenbach to explore other options, such as stone columns and deep-soil mixing, before deciding on CMM®. With this technique, you can vibrate the tube in very quickly, pour in the concrete and then lift the tube out – it’s around three times quicker than traditional piling methods.”
Having never before carried out rigid inclusions, the Franki team was able to demonstrate the wider group’s track record and assure the client it would have access to the skills and machinery to complete the task.
Global experts on site
The three-year project started on site in late 2016, with a superintendent and operator from Keller France coming over for the first few months to supervise and ensure the crew was well trained. New equipment was also brought in, including three Liebherr LRB 255 rigs equipped with ring vibrators – one brand new, one from France and one from Poland. A fourth – a new-model LRB 355 – was later added to increase productivity. Keller vibrocats made in-house will complete the equipment.
The project calls for more than 46,700 CMM® to be installed in grids of 2.5-3.5m in depths of 25m-38m. Using a vibratory driving method rather than auger allows operators to install lengths based on the actual ground profile, rather than on a single specific designed depth, which may be inadequate or over-conservative. The columns are finished with a gravel head – the value added by the Keller CMM® technology – and topped with 2-3m of engineered fill, which acts as a load-transfer platform. In addition to its structural advantages, the gravel head also reduces the risk of column damage by construction vehicles.
“Introducing a new technique has been very exciting for all of us and it’s all gone very smoothly,” adds Victor. “Being able to tap into the wider Keller expertise has given us a huge advantage. If we’d just been a local company without access to that expertise and machinery we wouldn’t have been able to do the job. It’s been a really successful team effort. We now have a new technique we can offer, potentially winning more significant projects like Clairwood.”