Thanks to rigorous planning, innovative thinking and group collaborations, Keller has worked with its client to preserve a historic building and ensure it remains the stunning centrepiece of a new multimillion-dollar retirement community.
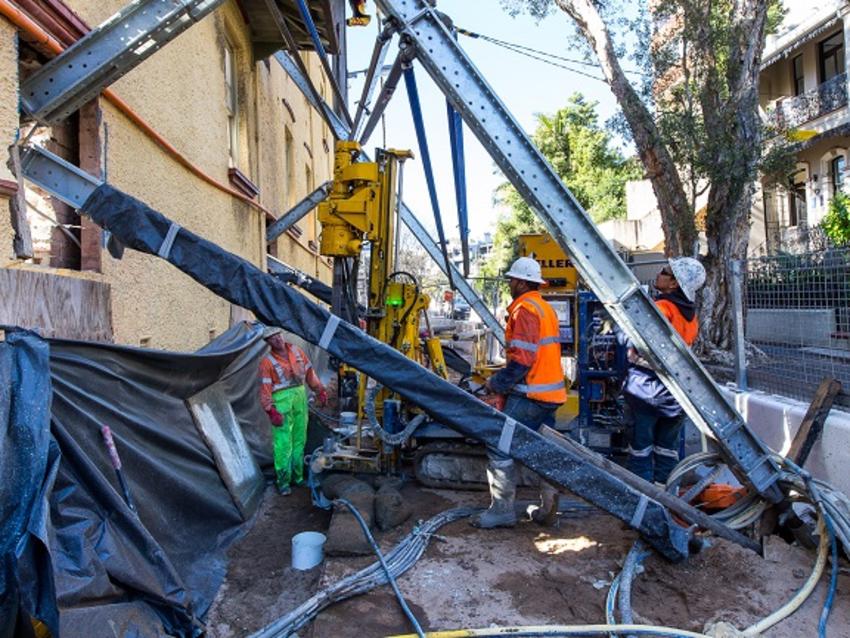
The Terraces is a A$180 million project to upgrade and extend a residential care unit, as well as construct luxury independent apartments for the over 55s.
The work’s taking place on the site of the Scottish Hospital, which dates back to the mid-1800s, in the upmarket suburb of Paddington. As part of the redevelopment, principle contractor Multiplex wanted to keep part of the characterful old building and make it an attractive part of this prestigious development.
However, the client faced problems at an early stage, when parts of the original building’s footings were shown to be deteriorating. As one of the world’s leading geotechnical companies – and having recently carried out similarly sensitive heritage work in Christchurch – Keller was approached to design a scheme to preserve the building.
Innovative solutions for a challenging site
“A complicated series of props needed to stay in place during the entire works and the proposed renovations increased the existing loads considerably, so it was a difficult design,” says Senior Project Engineer Damien Bray.
“Because we had to work around the structural props and in tight spaces, including doorways and metre-wide hallways, it was necessary to use the smallest jet-grouting and micropile rigs available,” he explains. These included a KB1 jet grout rig, designed and built in house by KGS. As the works were on the client’s critical path it was necessary to perform the micropiling and jet grouting concurrently, requiring careful planning and complicated material handling.
The works themselves included over a hundred jet grout underpinning columns, 60 vertical and inclined retaining micropiles, 51 foundation micropiles and a number of multi-strand soil anchors. Due to height constraints, the team could only drill 1m lengths for the majority of the site.
During the works it was also discovered that the rock level was up to double the depth to that originally designed for. This made constructing and installing the micropiles more complex, especially when working around structural props. Ingeniously, to overcome this, micropiles were specially designed to be coupled together on site before being installed using a limited access crane.
Tapping into our global expertise
“Due to the sensitivity of the structure it was specified that no more than 20mm settlement and 10mm lateral movement could occur," Damien explains. “As you can imagine, that’s difficult when you’re jet grouting and temporally liquifying the soil under a partially collapsed building, With little room for error, it was necessary to understand if any movement was occurring during or after any of the works had been completed. To reduce risk it was decided to engage [sister company] Getec in the UK to travel to Sydney to install a number of hydrostatic levelling cell.”
The specialist instrumentation was linked to a web-based system, providing real-time vertical movement monitoring during and post installation works. This introduced a level of confidence and understanding that all works were performed safely and without further damage to the building.
Damien admits that being trusted to save the historic building in such complex circumstances gave him “a few sleepless nights”, but thanks to a well-designed plan excellently executed, the project was completed successfully.
“This project demonstrated that we’re here to provide a solution that best meets a client’s needs, not our own,” Damien adds. “We listened, we reacted and we explored all the equipment, technology and materials at our disposal to come up with a bespoke solution. This shows we’re not just a contractor, but a complete service provider.”