When a large-scale railway improvement project in Poland hit the buffers due to a conflict over temporary closures, Keller came up with an ingenious idea to keep the works on the rails.
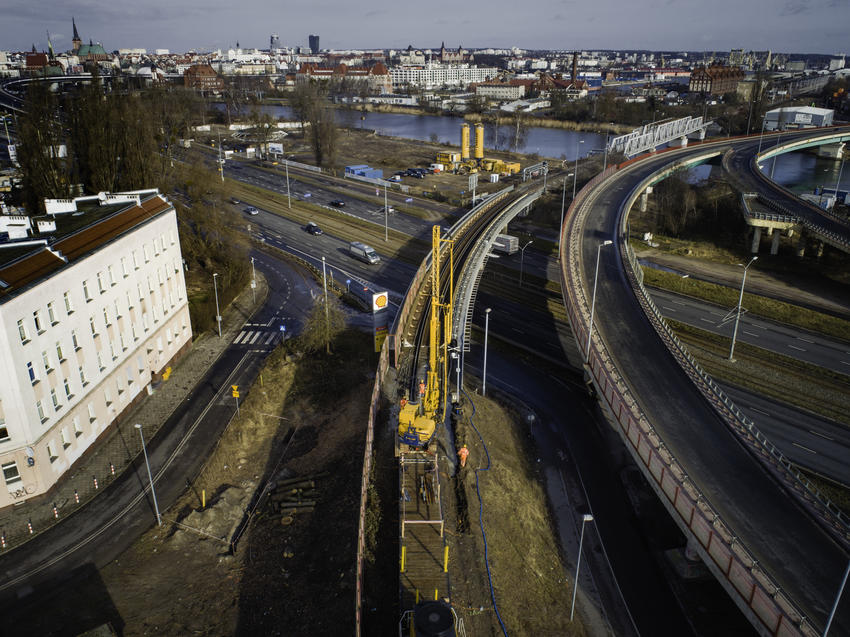
Located close to the Baltic Sea and German border, Szczecin is a major seaport and a catalyst for economic growth in north-west Poland. As such, the government is investing heavily in improving rail access to the port.
Keller was chosen by general contractor Torpol to be part of the upgrade, and tasked with constructing several hundred kilometres of jet-grouted columns across a surface area of around 350,000m2.
“Working on a railway site, especially one as large as this, is a genuine challenge in terms of organisation and logistics,” says Lech Danieluk, Keller Office Manager. “Managing the phasing, while working alongside tracks in operation and live power lines, not to mention countless conflicts with underground utilities, has made this an extremely challenging project.
“However, we’ve continued to meet the schedule by organising the works efficiently, which is down to close cooperation between ourselves and Torpol, as well as an active design process.”
Flexible approach
From the start, Keller recognised that improving such a large area would require an intelligent approach, one that could flexibly adapt to variations in soil condition and other obstacles.
“The design has almost been like a living organism, constantly evolving and changing,” says Lech. “Some changes have been minor, such as adjusting column layouts to avoid utilities, but others have been much more complex.”
For example, part of the project involves strengthening the subgrade soil for existing and new track beds on a small island called Ostrów Grabowski, home to many businesses that heavily rely on the rail network. The companies wanted the rail line to be closed for a much shorter time than both Keller and Torpol needed to complete the works, which included demolishing the existing track bed, preparing the working platform for the piling rigs, strengthening the soil and bridge abutments, and laying the new track bed.
A bright idea
With all parties at an impasse, the Keller team came up with an idea. “We call it the Geo-Train,” says Lech. “We put our drilling rig on a rail platform pushed along the track by a locomotive, and used a handcar to shuttle materials to it. This innovative solution reduced the amount of time needed to move the rig and the materials, minimising network downtime and speeding up the process.
It also had the advantage of enabling the crew to easily get off the tracks within a couple of hours and allow any unplanned freight trains to pass.
The work itself in this area involved installing jet-grout columns to reduce settlement of the existing railroad fill. Column spacing was adjusted to match the loads, with the lengths adapted to the prevailing soil conditions.
Importantly, the technology used to make the columns is shock- and vibration-free, so it didn’t affect the existing fill or track bed in any way. This meant that immediately after completing the work, trains were allowed to run again – albeit at reduced speed – without the need to adjust the track, which would have created further delays.
The Keller team are scheduled to complete the rest of the project by the end of this year.
More than just a job
“When we first tentatively suggested the idea of the Geo-Train, we weren’t expecting such a positive response, but everyone was on board immediately,” says Lech. “In fact, the idea has been so successful, we’re thinking of using it in another area where there’s a similar problem with temporary closures. In the meantime, our engineers and mechanics are making some modifications to ensure it runs even more smoothly.
“When you’re able to come up with an innovative solution such as this and you see everyone’s enthusiasm, you’re reminded how working for Keller is more than just a job. Providing customer satisfaction was something that gave everyone a boost.”