Keller teams across the world are doing everything they can to minimise the impact of the coronavirus outbreak and keep projects running safely wherever possible. In some cases that means going to extraordinary lengths, just to get to their sites.
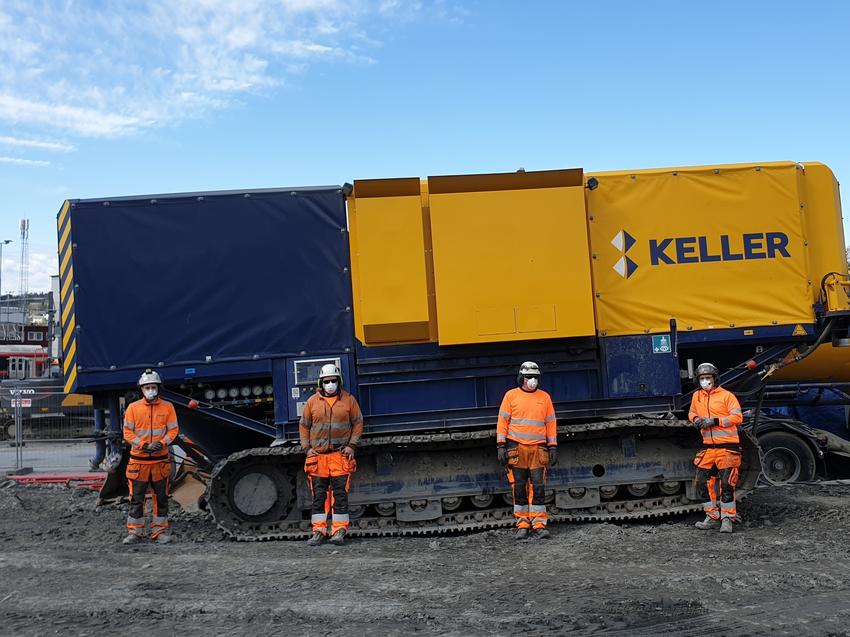
Sweden and Norway: EMEA employees rally to support vital projects
Over the past few weeks, skilled workers from Austria, Italy, Greece, Poland and Estonia have helped ensure key infrastructure projects in Scandinavia can go ahead – despite some logistically complicated journeys.
“It’s taken a lot of careful coordination and the support of two travel agencies to get the workers to the region as quickly as possible,” says Robert Thurner, General Manager for Sweden and Norway. These trips have included:
- 11 Austrians renting a car from southern Austria to Frankfurt, then flying to Stockholm and driving to Gothenburg – a 27-hour trip.
- Four Italians travelling via Zurich to Amsterdam or Frankfurt, then onto Oslo or Stockholm and Gothenburg. Those in Oslo have had to spend two weeks in quarantine.
- Four Poles taking a lengthy car journey and then a ferry to Stockholm and onto Gothenburg.
- Three Estonians coming via ferry to Stockholm and driving to Gothenburg.
- One Greek colleague driving from Thessaloniki to Athens, then flying to Zurich to Amsterdam and onto Gothenburg via Stockholm.
The projects they’ve been working on include the West Link rail tunnel under central Gothenburg, where Keller is carrying out deep soil mixing, jet grouting and uplift anchors; and a railway construction project in the Norwegian city of Moss.
“Although Sweden and Norway have approached the coronavirus outbreak differently, both countries have wanted to keep these major projects going,” says Robert. “Keller shares equipment and resources across EMEA so we needed these guys to be able to support that.
“Normally they would work two weeks on, one week off, but in this situation they’ve said they’re happy to stay here for six to eight weeks without going home if need be. I’m proud of the way the Keller family has pulled together so we can meet obligations.
“Other contractors here haven’t been able to react this way and for us it’s about showing our clients they have the right partner. We talk a lot about global strength and local focus at Keller, but this shows we can live up to that – even in the most difficult situations.”
Australia: Colleagues take 26-hour, 1,700km bus ride to get to work
Although Australia has largely got the Covid-19 outbreak under control, flight cancellations have made it difficult for some Keller employees to get to their project sites.
On 15 April, shortly after the Easter break, seven colleagues from Brisbane, Queensland boarded a coach to begin a lengthy, 26-hour journey to various sites in Melbourne, Victoria.
“They’d been working in Victoria before Easter and we were monitoring the situation closely,” explains Keller Australia’s Operations Director Tony Lansdown. “Things were changing fast with state border closures, but we’d been assured that if they went home to Queensland, they’d be able to get back again, as construction is considered essential. So they went home – and during the break the return flights were cancelled.”
With several projects ongoing in Victoria, Keller relies heavily on being able to move skilled workers around to meet demand. The workers were consulted with and were happy to go back to Melbourne via coach – despite the approximately 1,700km journey.
“We approached a couple of companies and made sure the company we chose had a robust Covid-19 management plan and risk assessment,” he adds. “We were very impressed with what they came back with.”
The 48-seater coach gave everyone plenty of room to space out and hand sanitiser was on board. To ensure the employees’ safety, the drivers swapped out at various intervals.
The group arrived safely in Melbourne, ensuring vital projects including the Westgate Tunnel and Escala Apartments have been able to keep going. While on site, all Keller employees are following strict distancing rules, including working in very small teams, using hand sanitiser and only attending pre-start meetings outdoors in groups of no more than eight. All shared equipment is cleaned thoroughly after use with an anti-bacterial spray.
“We’re doing everything we can to keep our projects running and meet client commitments, while maintaining employee safety,” says Tony.