Keller company HJ Foundation has once again delivered the goods on a challenging project – this time on the first phase of a major port expansion in south Florida.
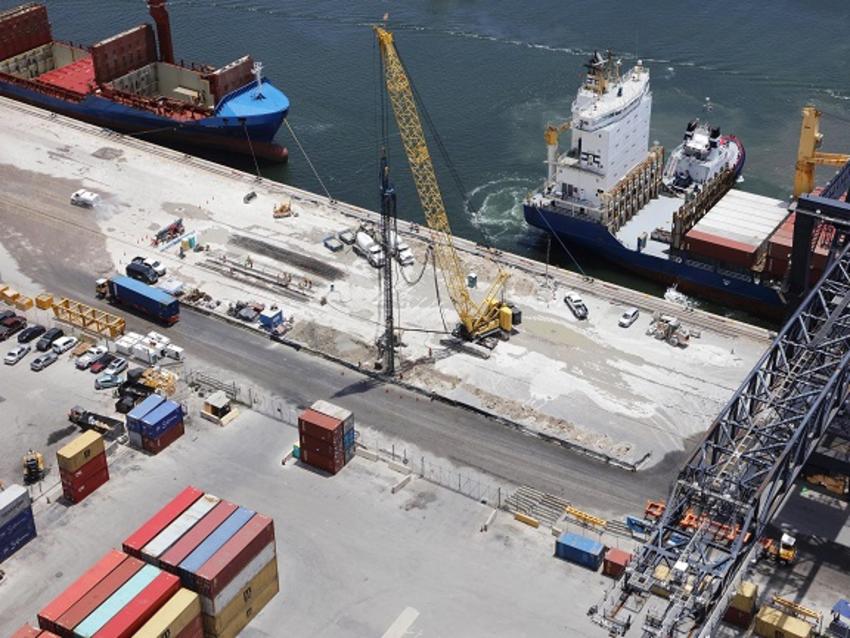
Port Everglades in Fort Lauderdale is the world’s third-busiest cruise port and the busiest container port in Florida, handling more than a million cargo containers every year.
A vital economic generator for the area, last year the port was given the go-ahead for a $437.5 million expansion to handle increasing demand. This will include lengthening the deepwater turnaround area, adding new berths for larger cargo ships and installing new crane rail infrastructure.
Known as the Southport Turning Notch Expansion, the project got underway earlier this year, with HJ Foundation appointed by general contractor Moss Kiewit to install more than 1,700 piles in three phases.
Keeping operational
“We were chosen for our engineering and operational expertise, our safety record, a competitive price and our proven ability to deliver large projects on time, to a high standard,” explains Senior Project Manager Andres Enciso.
Over the three phases HJ will install 1,741 augercast piles at diameters of 16, 18 and 24 inches, all up to 92ft long. The team recently finished installing 792 piles for phase one, and will return in 2020 and 2021 for the remaining stages.
“What made the first phase so challenging was that we had to install the piles while the port remained fully operational,” adds Andres. “So we worked closely with the contractor to rigorously coordinate the works and deliveries, ensuring port operations went uninterrupted and employees could safely access areas.
“This meant that we had to contain all the spoil and grout within very tightly confined work areas; not easy with such large rigs.”
Adding to the challenge, some piles needed to be installed where there were already existing structures and utilities. This required constant and clear communication between engineers, project management, field operations and Moss Kiewit to accommodate deviations and create quick redesigns. Around five percent of the piles were batter piles, installed at a 1:5 angle.
“A well-oiled machine”
“We successfully completed the first phase on time within 21 weeks without any safety incidents and with all the planned logistics and sequencing working well to ensure port operations ran safely and continuously,” adds Andres.
The client was happy too. John Ricker, Senior Superintendent at Moss Kiewit, says: “Once again I’ve been thoroughly impressed with the professionalism and dedicated manner that HJ employees go about their daily business. They are a true representation of a well-oiled machine. Efficient, safety-minded and always a pleasure to interact with.
“The complications on this project and the constant moving and reorganising was, to say the least, a serious challenge. This project had the makings of a disaster with all the underground obstructions, utilities and volatile shipping schedules, but when I heard HJ had landed the job, I had an immediate sense of relief.”