Keller companies HJ Foundation and Hayward Baker have developed an innovative solution that enables economical construction of larger, deeper basements in areas with a high underground water table. HJ Project Manager Nick Feldt explains the solution and the tremendous benefits it brings to our clients...
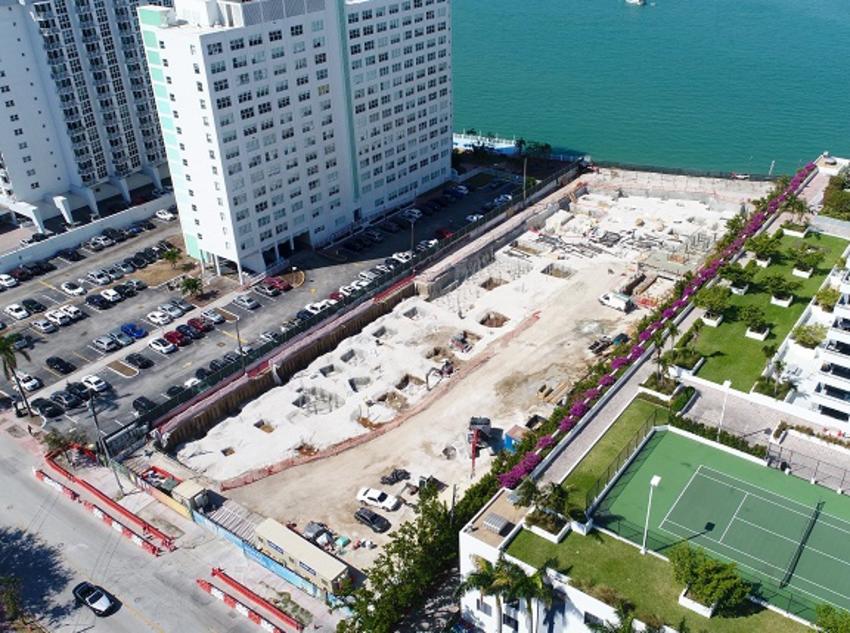
In a world where space is at a premium, going underground allows property developers to maximise their investment. In particular, constructing parking below ground is a space-saving solution that creates more sellable space above and a more architecturally attractive building.
In much of the US, where the water table is deep or the soils are less permeable, excavating basement space several storeys deep isn’t much of a challenge. But in South Florida where the water is just a couple of feet below the surface and soil and rock are highly permeable, construction companies face more of a challenge.
“Historically, when building basements in south Florida, contractors had to continuously pump tremendous amounts of water in the shallow groundwater, porous rock conditions.”
HJ Project Manager Nick Feldt says. “The difficulty is, as you go deeper, the pressure of the water increases and you get to a certain point where you no longer have enough power to pump all the water out, or a place to dispose of it.
“Because of environmental regulations, the water you’re pumping out has to be contained and reinjected on site and reinjection wells can only take so much. So, for developers in this area they’re really limited in how far underground they could go.”
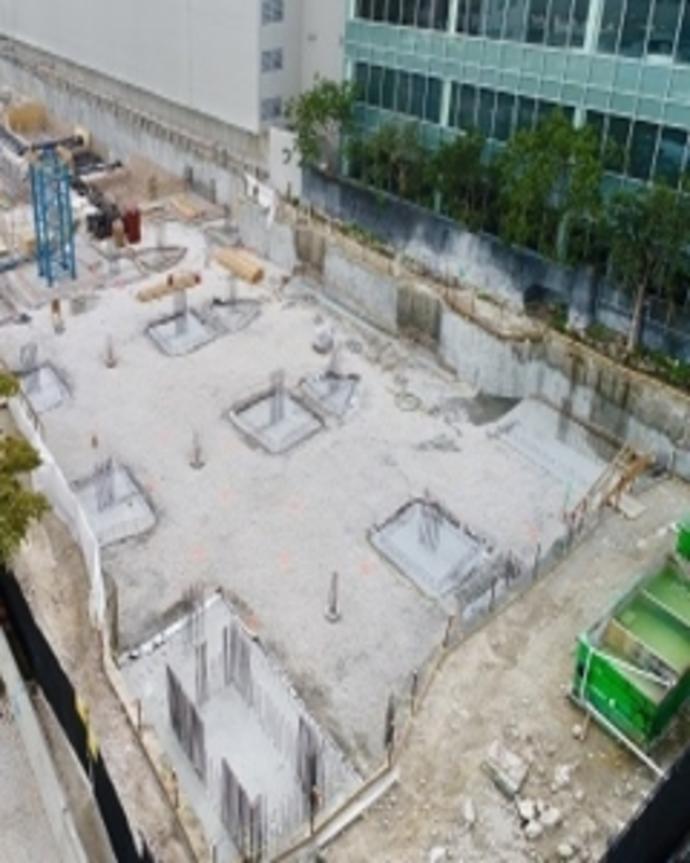
Guaranteed watertight solution
That’s changed, thanks to a joint venture between HJ Foundation and Hayward Baker. For the past six years the Keller business units have refined a solution that allows clients to create much larger basements, so far upwards of 127,000 square feet and up to three storeys underground, with deeper basements currently being proposed.
The principle techniques addressing the groundwater issues are soil mixing with CFA/augercast piles. This involves injecting cement slurry into the ground through a tool that simultaneously mixes it with the in-situ soil, creating a soilcrete material that’s strong and almost impermeable, anchored down with CFA/augercast piles. When applied to the perimeter and below the planned basement, the excavation can be performed with minimal seepage (less than a garden hose) from the sides and below.
One of the reasons it works so well in South Florida is because of the geological conditions. “The geology here is mostly sand and limestone. Our limestone has a lot of small, finger-sized interconnected voids. This makes it very permeable but also easier to be broken up and mixed,” Nick explains.
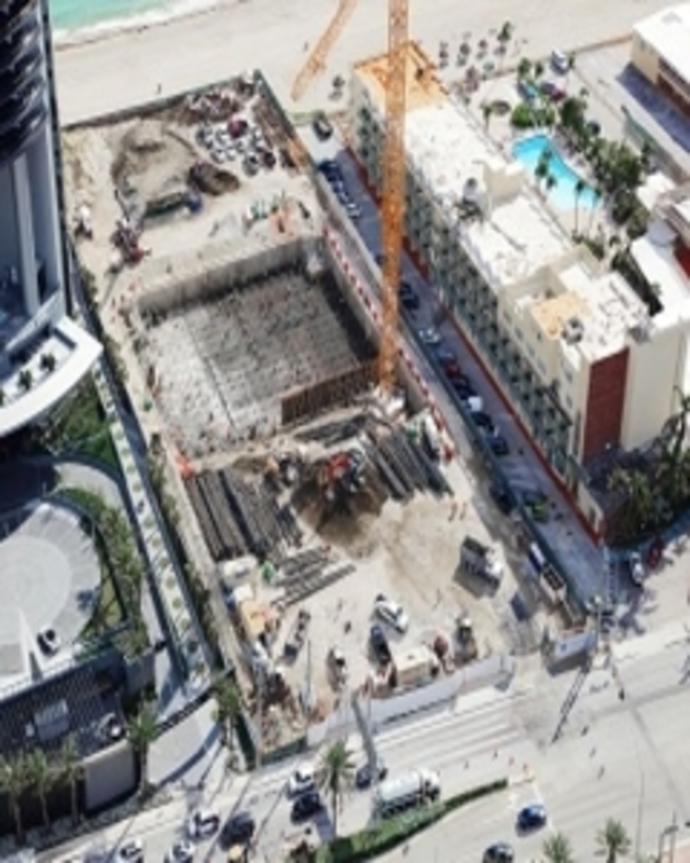
Combining expertise
The total solution combines Hayward Baker’s soil mixing with HJ Foundation’s augercast piling and site preparation/logistics abilities..
“Hayward Baker’s long-time expertise in soil mixing and HJ Foundation’s 30 years’ local augercast and site logistics experience, combined with the relationships built with suppliers, engineers, architects, other trades and clients, make for a powerful offering,” Nick adds.
“What really separates us from the competition though is the fact that we provide the guaranteed turnkey solution for clients. We offer a guaranteed price and schedule based on the contract documents and provide everything. This includes clearing the site, creating a safe work platform, constructing the deep-soil mix plug, installing the augercast piles to support the building, performing the basement excavation, cutting/chipping all the piles and managing any water seepage.
“While doing this, we provide all logistics including scheduling and coordinating these activities as well as all layout, as-builts, flagmen, safety – essentially taking the raw site and preparing it for the contractor to begin building the structure. All this is provided by a single company, Keller. That’s something our competitors don’t offer.”
The team is currently working on its 11th basement solution project and Nick says that, as word spreads, they’re becoming more and more common. “At first, clients are quite skeptical that we can build an excavation that deep and that dry, but when they see it they’re really impressed.”
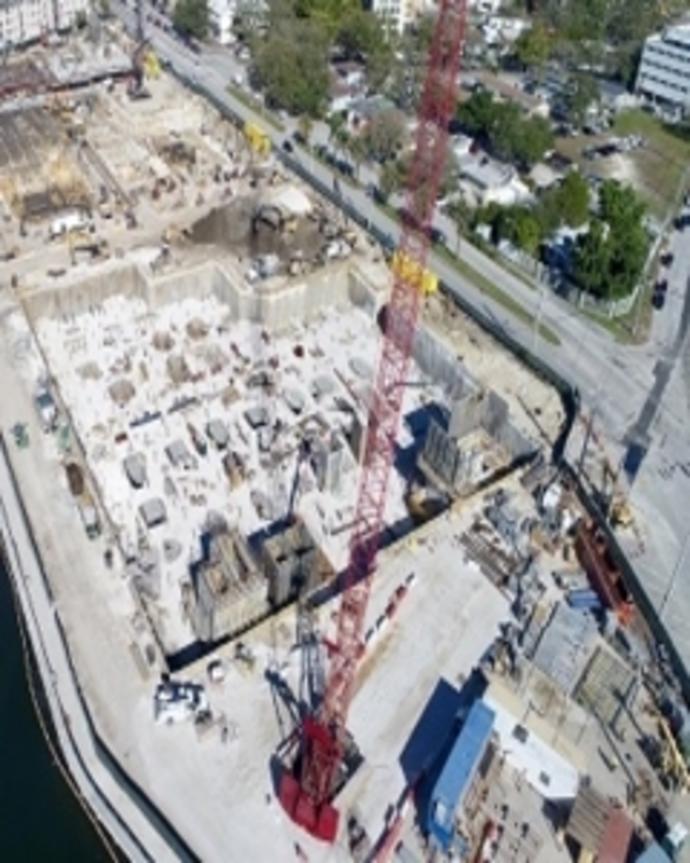
Spreading the word
To educate local engineers, developers and architects, HJ Foundation and Hayward Baker have held several events at hotels near the project sites. These include a presentation explaining the projects and Keller services, a site visit to active and completed projects and lunch.
“Over the last four years we’ve really refined this into a cost-effective, schedule-driven, guaranteed solution,” he says. “We started off with one project at a time and now we have three or four constantly on the go at different stages.
“It’s a guaranteed solution that really demonstrates Keller’s ability to innovate and offer something unique to our clients.”
What our clients say
Moss & Associates – Alexander Smith, Vice President: “The DSM system is working very well, and above our expectations.”
Coastal Construction – John Mills, Vice President of Operations: “Your team creates very dry holes; extremely dry holes.”
West Avenue Neighbourhood Association – Shawn Patrick Bryant, Board Member: “They are doing an excellent job of maintaining the area. Even more important, they are maintaining a safe area.”
Coastal Construction – Chris Christy, Director of Pre-construction: “HJ Foundation is a highly professional company. They are a great asset providing guaranteed results.”
Cetco Hydro-Shield Waterproofing – David K Gehlbach, Territory Sales Manager: “[Keller] has performed and continues to perform, high-quality work keeping the project on time and within budget.”
Current projects using deep soil mix plugs
- River Landing
Shops and residential development
Scope:
- 62,000ft2 of deep soil mix plug (excavation of foundation approx 60,000 cubic yards)
- 1,800ft of twin soil mix walls
- 1400+ augercast piles 14-in to 24in diameter and up to 65ft deep
The soil mix technique allowed for the construction of an underground parking garage, 15ft below the water table, with minimal dewatering (less than 50 gallons per minute) next to the Miami River.
- Optima Plaza North
Office block
Scope:
- 63,000ft2 of deep soil mix plug (excavation of foundation approx 48,000 cubic yards)
- 1,900ft of twin soil mix walls
- 500+ augercast piles 18in to 24in diameter and up to 60ft deep
The soil mix technique allowed for the construction of an underground parking garage, 8ft below the water table, with minimal dewatering (less than 50gpm).
- Turnberry Ocean Club
Luxury condo
Scope:
- 57,000ft2 of deep soil mix plug (excavation of foundation approx 50,000 cubic yards)
- 1,000ft of twin soil mix walls
- 300+ 30in augercast piles up to 160ft
- 70+ 16in augercast piles up to 50ft
The soil mix technique will allow for the construction of an underground parking garage next to the Miami Bay, 12ft below the water table, with minimal dewatering efforts.
- Monad Terrace
Luxury condo
Scope:
- 50,000ft2 of deep soil mix plug (excavation of foundation approx 30,000 cubic yards)
- 1,100ft of twin soil mix walls
- 500+ 30in augercast piles 18in-24in diameter and up to 75ft deep
- 233 24in augercast piles up to 75ft
- 256 18in augercast piles up to 75ft
The soil mix technique will allow for the construction of an underground parking garage next to the Miami Bay, 12ft below the water table, with minimal dewatering efforts.